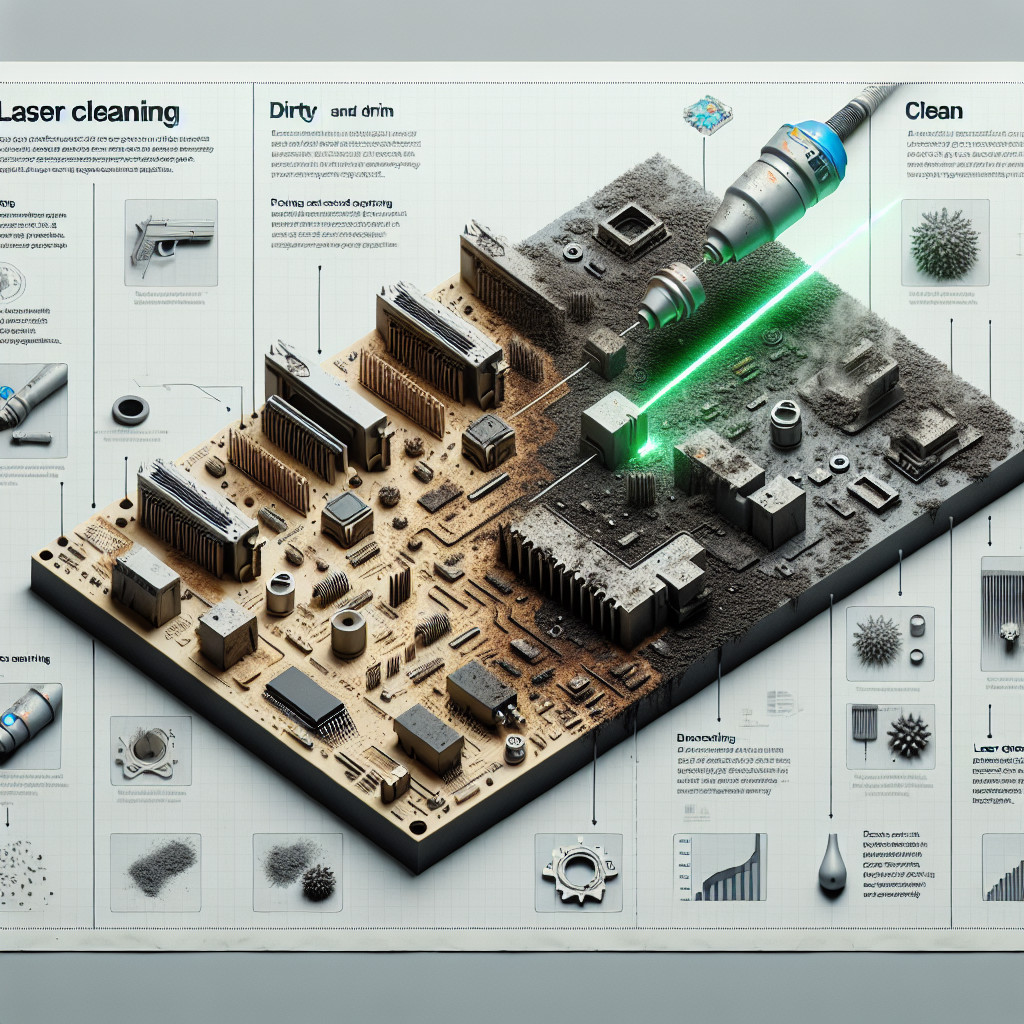
Laser cleaning for removing contaminants from electronic components
- Introduction to laser cleaning technology
- Types of contaminants on electronic components
- Benefits of laser cleaning for electronic components
- Comparison of laser cleaning with traditional cleaning methods
- Factors to consider when choosing laser cleaning for electronic components
Introduction to laser cleaning technology
One of the key advantages of laser cleaning technology is its precision and control. The laser beam can be precisely focused on the target area, allowing for selective removal of contaminants without damaging the underlying surface. This level of precision is particularly useful in industries such as aerospace, automotive, and electronics, where cleanliness and surface quality are critical.
Another advantage of laser cleaning technology is its versatility. It can be used on a wide range of materials, including metals, plastics, ceramics, and composites. This makes it a valuable tool for a variety of applications, from removing paint and coatings from metal surfaces to cleaning delicate electronic components.
In addition to its precision and versatility, laser cleaning technology is also environmentally friendly. Unlike traditional cleaning methods that use harsh chemicals or abrasive materials, laser cleaning does not produce any waste or harmful byproducts. This makes it a sustainable and eco-friendly option for industries looking to reduce their environmental impact.
The process of laser cleaning involves directing a high-energy laser beam onto the surface to be cleaned. The laser beam heats up and vaporizes the contaminants, which are then removed by a vacuum system or blown away by compressed air. The intensity and duration of the laser beam can be adjusted to suit the specific cleaning requirements, making it a highly customizable and efficient process.
To illustrate the effectiveness of laser cleaning technology, let’s consider a practical example. Imagine a metal surface that is covered in rust and corrosion. Traditional cleaning methods such as sandblasting or chemical treatments may be effective, but they can also damage the underlying metal and create waste products that need to be disposed of properly. In contrast, laser cleaning can selectively remove the rust and corrosion without damaging the metal surface, leaving behind a clean and restored surface.
In conclusion, laser cleaning technology is a powerful and versatile method for removing contaminants and unwanted materials from surfaces. Its precision, control, and environmental friendliness make it an attractive option for industries looking to improve their cleaning processes. As technology continues to advance, we can expect to see even more applications for laser cleaning in a wide range of industries.
Types of contaminants on electronic components
1. Dust and dirt
Dust and dirt are common contaminants that can accumulate on electronic components over time. They can block airflow and cause overheating, leading to performance issues and potential damage to the components.
2. Moisture
Moisture is another common contaminant that can cause corrosion and short circuits on electronic components. It can also lead to the growth of mold and mildew, which can further damage the components.
3. Chemicals
Chemicals such as cleaning solvents, oils, and other substances can also contaminate electronic components. These chemicals can cause corrosion, short circuits, and other issues that can affect the performance of the components.
4. Static electricity
Static electricity can build up on electronic components and discharge, causing damage to the components. It is important to handle electronic components carefully to prevent static electricity from causing damage.
5. Solder flux residue
Solder flux residue is a common contaminant that can be left behind on electronic components after soldering. This residue can cause corrosion and affect the performance of the components if not properly cleaned off.
6. Particulate contamination
Particulate contamination refers to small particles that can contaminate electronic components. These particles can cause short circuits, block airflow, and lead to overheating if not removed from the components.
7. ESD (Electrostatic Discharge)
ESD is a sudden flow of electricity between two electrically charged objects caused by contact, an electrical short, or dielectric breakdown. ESD can damage electronic components and affect their performance if not properly controlled.
8. Biological contaminants
Biological contaminants such as mold, mildew, and bacteria can also affect electronic components. These contaminants can cause corrosion, short circuits, and other issues that can affect the performance of the components.
Overall, it is important to be aware of the different types of contaminants that can affect electronic components and take steps to prevent them from causing damage. Proper handling, storage, and cleaning of electronic components can help ensure their proper functioning and longevity.
Benefits of laser cleaning for electronic components
What is laser cleaning?
Laser cleaning is a non-contact, non-abrasive cleaning method that uses a high-energy laser beam to remove contaminants from surfaces. It is a highly precise and efficient cleaning method that can be used on a wide range of materials, including electronic components.
- Efficiency – Laser cleaning is a highly efficient cleaning method that can remove contaminants quickly and effectively, without damaging the electronic components.
- Precision – Laser cleaning is a precise cleaning method that can target specific areas on electronic components, ensuring thorough cleaning without affecting other parts.
- Non-contact – Laser cleaning is a non-contact cleaning method, which means that there is no physical contact between the cleaning tool and the electronic components. This reduces the risk of damage to the components.
- Non-abrasive – Laser cleaning is a non-abrasive cleaning method, which means that it does not use any harsh chemicals or abrasive materials that can damage the electronic components.
- Environmentally friendly – Laser cleaning is an environmentally friendly cleaning method that does not produce any harmful waste or emissions.
- Cost-effective – Laser cleaning is a cost-effective cleaning method that can help prolong the lifespan of electronic components, reducing the need for frequent replacements.
Applications of laser cleaning for electronic components
Laser cleaning can be used for a wide range of electronic components, including:
- Printed circuit boards
- Microchips
- Connectors
- Sensors
- Optical components
Overall, laser cleaning is a highly efficient, precise, and environmentally friendly cleaning method that can help prolong the lifespan of electronic components and ensure optimal performance. It is a cost-effective cleaning solution that is becoming increasingly popular in the electronics industry.
Comparison of laser cleaning with traditional cleaning methods
Laser Cleaning
Laser cleaning is a non-contact method of cleaning surfaces using a laser beam. The laser beam is directed at the surface to be cleaned, and the energy from the laser beam vaporizes or ablates the contaminants on the surface. This method is highly effective at removing dirt, rust, paint, and other contaminants from surfaces.
Advantages of Laser Cleaning
Advantages | Description |
---|---|
Non-contact | Laser cleaning is a non-contact method, which means that there is no physical contact between the cleaning equipment and the surface being cleaned. This reduces the risk of damage to the surface. |
Precision | Laser cleaning is a highly precise method, allowing for the removal of contaminants without affecting the underlying material. This makes it ideal for cleaning delicate surfaces. |
Environmentally friendly | Laser cleaning does not require the use of chemicals or solvents, making it an environmentally friendly cleaning method. |
Traditional Cleaning Methods
Traditional cleaning methods, such as scrubbing, sandblasting, and chemical cleaning, involve physical contact with the surface being cleaned. These methods are effective at removing contaminants, but they can also be abrasive and damaging to the surface.
Advantages of Traditional Cleaning Methods
Advantages | Description |
---|---|
Cost-effective | Traditional cleaning methods are often more cost-effective than laser cleaning, as they do not require specialized equipment. |
Versatile | Traditional cleaning methods can be used on a wide range of surfaces and materials. |
High cleaning power | Traditional cleaning methods can be highly effective at removing tough contaminants from surfaces. |
Conclusion
In conclusion, both laser cleaning and traditional cleaning methods have their advantages and disadvantages. Laser cleaning is a non-contact, precise, and environmentally friendly method of cleaning surfaces, but it can be more expensive than traditional cleaning methods. Traditional cleaning methods are cost-effective and versatile, but they can be abrasive and damaging to surfaces. The choice of cleaning method will depend on the specific requirements of the cleaning task.
Factors to consider when choosing laser cleaning for electronic components
1. Material compatibility
One of the most important factors to consider when choosing laser cleaning for electronic components is the compatibility of the material with the laser cleaning process. Different materials react differently to laser cleaning, so it is essential to ensure that the material of the electronic component can withstand the laser cleaning process without being damaged.
2. Power and wavelength
The power and wavelength of the laser used for cleaning electronic components are crucial factors to consider. The power of the laser determines how effectively it can remove contaminants from the surface of the electronic component, while the wavelength determines the depth of penetration into the material. It is important to choose a laser with the right power and wavelength for the specific cleaning requirements of the electronic component.
3. Precision and control
Another important factor to consider when choosing laser cleaning for electronic components is the level of precision and control offered by the laser cleaning system. The ability to precisely target and remove contaminants from the surface of the electronic component is essential for achieving optimal cleaning results without damaging the component itself.
4. Safety considerations
When using laser cleaning for electronic components, it is important to consider safety factors such as the emission of hazardous fumes and the risk of eye damage from the laser beam. It is essential to use appropriate safety measures and equipment to protect both the operator and the electronic components being cleaned.
5. Cost and efficiency
Finally, cost and efficiency are important factors to consider when choosing laser cleaning for electronic components. While laser cleaning can be a more expensive option compared to traditional cleaning methods, it offers greater efficiency and precision, which can ultimately lead to cost savings in the long run. It is important to weigh the cost of laser cleaning against the benefits it offers in terms of cleaning effectiveness and component longevity.
Conclusion
Choosing laser cleaning for electronic components can offer numerous benefits in terms of precision, efficiency, and effectiveness. However, it is essential to consider factors such as material compatibility, power and wavelength, precision and control, safety considerations, and cost and efficiency when selecting a laser cleaning system for electronic components. By keeping these factors in mind, you can ensure optimal cleaning results and prolong the lifespan of your electronic components.
Jeśli interesują Cię tanie sponsorowane publikacje SEO bez pośredników - skontaktuj się z nami:
Tel. 511 005 551
Email: biuro@codeengineers.com
- Laser cleaning for removing contaminants from electronic components - 16 July 2024
- How to prepare an IT project specification - 11 April 2024
- Kanban vs Scrum – which method to choose? - 12 January 2024

Piotr Kulik
Nazywam się Piotr Kulik i jestem specjalistą SEO, Google Ads i Analytics. Posiadam certyfikaty Google z zakresu reklamy i analityki oraz doświadczenie w pozycjonowaniu stron oraz sklepów internetowych. Jeśli interesują Cię tanie sponsorowane publikacje SEO bez pośredników - skontaktuj się z nami: Tel. 511 005 551 Email: biuro@codeengineers.com

WebMakers Spring Party 2022
You May Also Like
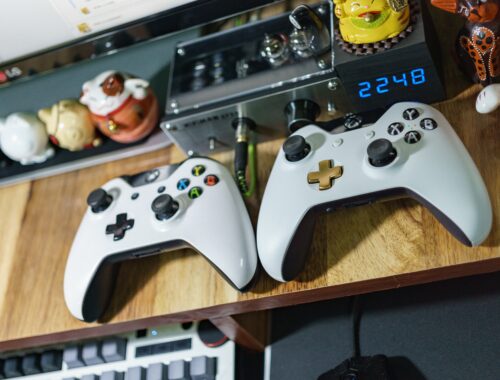
Cheap trinkets from China – what popular gadgets are worth investing in
5 February 2021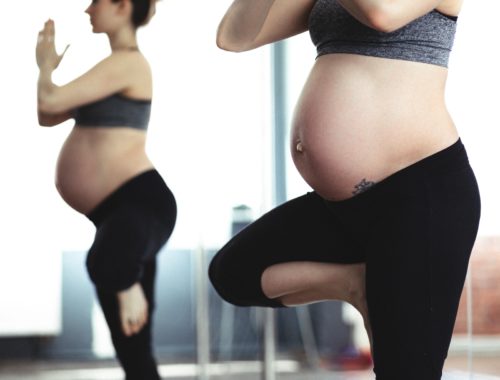
Trousers for pregnant women – put on comfort
2 February 2021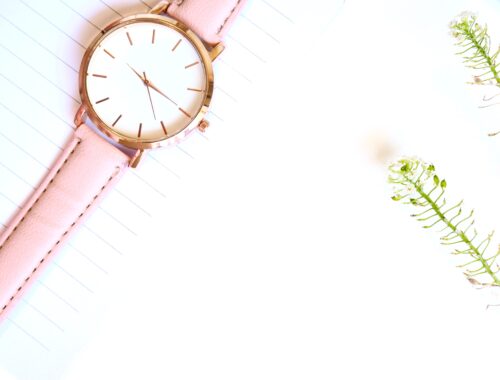